Don't miss our holiday offer - 30% OFF!
Comparative Analysis Of Single Toggle And Double Toggle Jaw Crushers: Assessing Cost-Efficiency And Operational Benefits
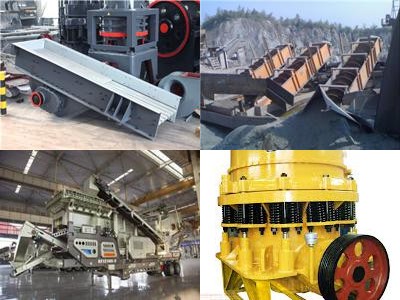
In the realm of heavy industrial equipment, jaw crushers stand as pivotal components in various sectors, from mining to construction. As a leading provider of crushers, mills, and other essential machinery, Zenith company delves into the intricacies of single toggle and double toggle jaw crushers, offering insights into their cost-efficiency and operational benefits. This article aims to guide industry professionals in making informed decisions regarding the optimal jaw crusher for their specific needs.
Introduction to Jaw Crushers: Types and Applications
Jaw crushers are fundamental in breaking down large rocks into smaller pieces, making them indispensable in the construction and mining industries. The primary distinction lies between single toggle and double toggle jaw crushers, each with unique advantages. Single toggle crushers are known for their simplicity and lower initial costs, while double toggle crushers offer more consistent crushing and are beneficial for harder materials. Common applications range from quarrying to recycling, where the choice of crusher significantly impacts efficiency and productivity.
Technical Comparison: Single Toggle vs Double Toggle
The mechanism of operation differs fundamentally between the two types. Single toggle jaw crushers utilize a single toggle plate that causes the lower part of the jaw to oscillate, whereas double toggle crushers have two toggles, adding to the complexity and cost but providing a more uniform crushing action. Design and structural differences also influence the choice; single toggles are lighter and more compact, making them easier to install and operate. However, double toggle jaw crushers excel in handling tougher materials, offering higher throughput capacities but at the expense of increased size and weight.
Cost-Efficiency Analysis: Initial Investment and Operational Costs
From a cost-efficiency perspective, single toggle jaw crushers generally have a lower initial investment, making them an attractive option for businesses looking to minimize upfront costs. However, the long-term operational costs, including maintenance, repair, and energy consumption, can vary significantly. Double toggle jaw crushers, while more expensive initially, may offer lower maintenance costs and better energy efficiency, translating to savings over the crusher’s lifespan. Zenith company provides a range of both single and double toggle crushers, ensuring options are available to meet various budgetary and operational requirements.
Operational Benefits and Limitations
When considering the operational benefits and limitations, the suitability for different materials and sizes becomes a critical factor. Single toggle crushers are often preferred for softer materials and smaller feed sizes, offering ease of maintenance and repair. In contrast, double toggle crushers are better suited for harder materials and larger feed sizes, providing enhanced durability and longevity. Zenith company’s extensive portfolio includes models designed for optimal performance across a wide range of applications, ensuring that every client finds the perfect match for their specific needs.
The choice between single toggle and double toggle jaw crushers involves a comprehensive analysis of cost-efficiency, operational benefits, and specific application requirements. Zenith company, with its vast selection of heavy industrial equipment, stands ready to assist customers in selecting the ideal jaw crusher that aligns with their operational goals and budgetary constraints. Whether the priority is initial cost savings with a single toggle or the enhanced performance characteristics of a double toggle, Zenith offers solutions that promise to enhance productivity and efficiency in any industrial setting.