Don't miss our holiday offer - 30% OFF!
How Does The Concave Affect The Performance Of A Cone Crusher?
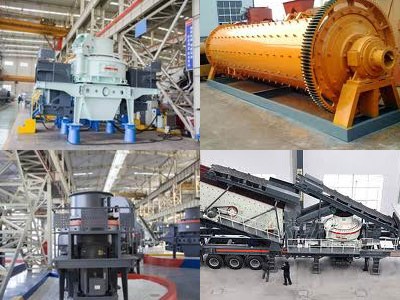
Understanding the Concave Design
Cone crushers are pivotal in the mining and construction industries, tasked with breaking down large rocks into smaller, more manageable sizes. Central to their operation is the concave, a crucial component nestled within the crusher’s crushing chamber. Acting as a protective shell, the concave plays a vital role in shaping the chamber for efficient crushing.
The concave’s significance lies in its ability to create a controlled space where rocks are crushed. Positioned above the mantle, the concave forms the upper portion of the crushing chamber. Its design directly influences the crusher’s performance, affecting factors such as throughput, particle size distribution, and energy consumption. Understanding the intricacies of concave design is paramount for maximizing cone crusher efficiency.
Understanding the Concave Design
The concave’s primary function is to provide a surface against which the incoming feed material is crushed. Its shape and configuration significantly impact the crushing process. Concaves with a steeper angle facilitate finer crushing, while shallower angles may promote coarser particle sizes. Additionally, the curvature of the concave affects the trajectory of the material, influencing the efficiency of the crushing action.
Moreover, the concave acts as a protective shield for the crusher’s mantle, guarding against premature wear and damage. Its strategic positioning ensures that the mantle remains intact and operational, prolonging the lifespan of the crusher. Therefore, selecting the appropriate concave design is essential for optimizing crusher performance and longevity.
Impact of Concave Geometry
Various factors contribute to the overall performance of a cone crusher, with concave geometry playing a pivotal role. The shape, angle, and material composition of the concave all influence the crushing process. Different designs can affect the distribution of stresses within the crusher, impacting wear rates and energy consumption.
For instance, a concave with a more pronounced curvature may generate higher crushing forces, leading to improved particle reduction. Conversely, concaves with flatter profiles may result in reduced throughput but higher product quality. Manufacturers often offer a range of concave options to accommodate different crushing needs, allowing operators to tailor their equipment for specific applications.
Optimizing Crusher Efficiency
To enhance crusher productivity and efficiency, careful consideration must be given to concave selection and maintenance. Choosing the right concave profile and material is crucial for achieving desired performance outcomes. Regular inspections and adjustments are also essential for ensuring optimal crusher operation.
Zenith offers a comprehensive range of cone crusher concaves designed to meet varying crushing demands. From standard designs to custom configurations, our concaves are engineered for durability and performance. With our expertise in heavy industrial equipment, we provide tailored solutions to maximize crusher efficiency and productivity.