Don't miss our holiday offer - 30% OFF!
Jaw Crusher Vs Cone Crusher: Which One Should You Choose?
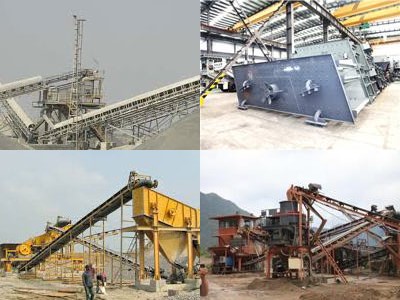
Welcome to our comprehensive guide comparing jaw crushers and cone crushers: two essential pieces of heavy industrial equipment in the world of crushing and material processing. As Zenith, a leading provider of crushers, mills, and other machinery for various industries, we understand the importance of making informed decisions when it comes to selecting the right equipment for your specific needs. In this article, we will delve into the intricacies of jaw crushers and cone crushers, exploring their differences, factors to consider when choosing between them, and real-world case studies to aid in decision-making.
Introduction to Jaw Crushers and Cone Crushers
Jaw crushers and cone crushers are both widely used in the mining, construction, and recycling industries to break down large rocks, ores, and other materials into smaller, more manageable pieces. Jaw crushers operate by compressing materials between a fixed jaw and a moving jaw, while cone crushers use a rotating mantle within a concave bowl to exert pressure on the material, crushing it against the bowl’s walls. Zenith offers a range of jaw crushers, including the PE series and the C6X series, known for their robust construction and high efficiency. For cone crushers, our offerings include the HST series and the HP series, designed for superior performance and reliability in various applications.
Key Differences Between Jaw Crushers and Cone Crushers
One of the primary distinctions between jaw crushers and cone crushers lies in their crushing mechanism. While jaw crushers exert pressure by compressing the material between two jaws, cone crushers utilize a rotating mantle and concave to achieve crushing action. This fundamental difference results in varying particle shapes and sizes produced by each type of crusher. Additionally, jaw crushers are generally more suitable for coarse crushing, whereas cone crushers excel in finer crushing applications. Zenith’s jaw crushers are ideal for primary crushing tasks, while our cone crushers are well-suited for secondary and tertiary crushing stages.
Factors to Consider When Choosing Between the Two
When deciding between a jaw crusher and a cone crusher, several factors come into play to ensure optimal performance and cost-effectiveness. Considerations include the type of material to be crushed, the required particle size, the desired throughput capacity, and the operating conditions. For instance, if you need to crush abrasive materials or achieve a finer product, a cone crusher may be the better choice. On the other hand, for primary crushing of hard, tough materials, a jaw crusher might be more suitable. Zenith’s expert team can assist you in evaluating these factors and selecting the most suitable crusher for your specific application.
Case Studies: Practical Applications and Decisions
To illustrate the practical implications of choosing between jaw crushers and cone crushers, let’s examine real-world case studies from various industries. These case studies will highlight the diverse applications of each type of crusher and provide insights into the decision-making process. Whether it’s achieving higher production rates, reducing maintenance costs, or improving overall efficiency, Zenith’s range of crushers offers solutions tailored to meet the unique requirements of our customers.
In conclusion, the choice between a jaw crusher and a cone crusher depends on various factors such as the type of material, desired particle size, and application requirements. As a trusted provider of industrial equipment, Zenith offers a wide range of high-quality jaw crushers and cone crushers to suit different needs. Whether you’re in mining, construction, or recycling, we have the expertise and solutions to help you make the right choice. Contact us today to learn more about our products and how they can benefit your operations.