Don't miss our holiday offer - 30% OFF!
Maximizing Output: The Impact Of 3-Inch Input Stone Size On 12X24 Jaw Crusher Production
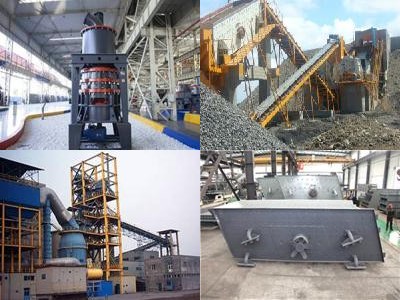
In the realm of construction and mining, the efficiency of crushing equipment is paramount for operational success and profitability. At Zenith Company, we understand the critical role that machinery plays in achieving these goals. This article delves into the intricacies of maximizing output with a specific focus on the impact of 3-inch input stone size on 12×24 jaw crusher production. Our expertise in manufacturing crushers, mills, and other heavy industrial equipment positions us uniquely to offer insights and recommendations for optimizing your crushing operations.
Understanding the 12×24 Jaw Crusher Mechanism
The 12×24 jaw crusher operates on a simple principle but is highly effective in breaking down large rocks into smaller, manageable sizes. The process involves the rock being fed into the crusher where it’s firmly clamped and then crushed between a fixed and a moving jaw. The key components, including the flywheel, toggle plates, and the jaw plates, play pivotal roles in the crushing process. The input size of the stone significantly affects the crusher’s overall performance, with the optimal size ensuring efficient operation and reduced wear on the crusher components.
The significance of maintaining the correct input size cannot be overstated. A 3-inch stone input is considered ideal for a 12×24 jaw crusher, balancing between the size of the stone that can be processed efficiently and the output size that meets the requirements for further processing or use. This balance is crucial for maximizing the crusher’s throughput and minimizing mechanical stress.
The Significance of 3-Inch Stone Input
Introducing a 3-inch stone input into a 12×24 jaw crusher significantly impacts crushing efficiency. This size is large enough to be handled efficiently by the crusher, yet small enough to minimize the strain on mechanical components, leading to a smoother operation and longer lifespan of the equipment. Adjustments may be necessary to accommodate this specific input size, including the settings of the jaw gap and the speed of operation, to ensure optimal processing.
Comparing the output with different input sizes reveals a clear advantage of the 3-inch stone. Smaller stones might pass through the crusher without being adequately crushed, while larger stones could cause jams and excessive wear. Thus, the 3-inch size represents a sweet spot for maximizing production efficiency and quality of the final product.
Strategies for Maximizing Production Output
To achieve the highest production output from a 12×24 jaw crusher, several strategies can be employed. Firstly, ensuring the crusher is set to the optimal settings for a 3-inch stone input is crucial. This involves adjusting the jaw gap to the correct width and optimizing the speed of the crusher. Regular maintenance is also vital to keep the crusher running smoothly and consistently. This includes routine checks and replacement of wear parts to prevent unexpected downtime.
Drawing from case studies, we’ve seen that operations that adhere to these strategies experience a significant increase in production output and a decrease in operational costs. Success stories from our clients at Zenith Company, who have implemented these adjustments, serve as a testament to the effectiveness of these strategies.
Maximizing the output of a 12×24 jaw crusher with a 3-inch stone input is not just about the right equipment; it’s about understanding the mechanism, the significance of the input size, and employing the right strategies for maintenance and operation. At Zenith Company, we pride ourselves on providing not just the equipment, such as our state-of-the-art jaw crushers and mills, but also the expertise and support necessary to optimize your production processes. By focusing on the key aspects outlined in this article, businesses can achieve higher efficiency, reduced operational costs, and ultimately, greater profitability.