Don't miss our holiday offer - 30% OFF!
Optimizing Performance: Understanding Cone Settings In Jaw Crushers
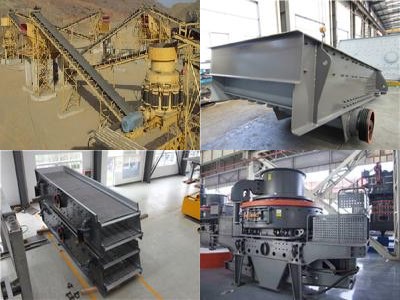
In the realm of heavy industrial equipment, optimizing machinery for peak performance is paramount. Zenith company, a leader in providing top-tier crushers, mills, and other essential tools, presents an insightful exploration into the optimization of cone settings in jaw crushers. This article delves into the intricacies of jaw crushers, highlighting the pivotal role of cone settings in enhancing operational efficiency and productivity. Join us as we navigate through the mechanics, adjustments, and strategic monitoring of cone settings to maximize performance.
Introduction to Jaw Crushers and Cone Settings
Jaw crushers are fundamental in the mining, construction, and demolition recycling industries, breaking down large rocks into smaller, manageable sizes. The cone settings within these crushers play a crucial role in determining the final size and quality of the output. Optimizing these settings is essential for improving crushing efficiency and reducing operational costs. This article aims to provide a comprehensive understanding of cone settings and their impact on jaw crusher performance.
Understanding the Mechanics of Jaw Crushers
At the heart of a jaw crusher is a pair of vertical jaws, one stationary and the other moving in a V alignment. The cone settings, adjustable gaps between the jaws, dictate the size of the material output. Precise adjustments to these settings can significantly influence the crushing process, enhancing both efficiency and product quality. Conversely, incorrect settings can lead to reduced productivity, increased wear on components, and higher operational costs.
Key Cone Settings in Jaw Crushers and Their Effects
The cone settings in jaw crushers, including the closed side setting (CSS) and open side setting (OSS), are critical for optimizing performance. Adjusting the CSS and OSS affects the final product size and throughput. For instance, a tighter CSS results in smaller output size but may reduce throughput. Understanding the balance and effects of these settings is crucial for operational efficiency. Real-world adjustments, based on material characteristics and desired output, demonstrate the tangible benefits of optimal cone settings.
Step-by-Step Guide to Adjusting Cone Settings
Adjusting cone settings requires careful preparation and precision. Safety is paramount; ensure all safety protocols are followed and the equipment is properly secured. Begin with a thorough inspection of the crusher and identify the necessary adjustments. Detailed instructions for common adjustments include measuring the current settings, making incremental changes, and verifying the impact on output. Precision in these adjustments ensures optimal performance and longevity of the crusher.
Maximizing Performance Through Optimal Cone Settings
Regular monitoring and strategic adjustments of cone settings are essential for maintaining peak performance. Implementing a routine inspection and adjustment program can lead to significant improvements in efficiency and productivity. Case studies from Zenith customers highlight the positive impact of optimized cone settings on operational outcomes. Looking ahead, advancements in technology promise even greater control and precision in adjusting cone settings, further enhancing crusher performance.
The optimization of cone settings in jaw crushers is a critical aspect of operational efficiency and productivity. Zenith company, with its extensive expertise and range of high-quality crushers, mills, and heavy industrial equipment, is at the forefront of providing solutions that meet the evolving needs of the industry. By understanding and implementing the principles outlined in this article, businesses can achieve significant performance improvements, ensuring their operations are both efficient and cost-effective.