Don't miss our holiday offer - 30% OFF!
Understanding The Importance Of Crusher Wear Plates: Enhancing Equipment Performance And Longevity
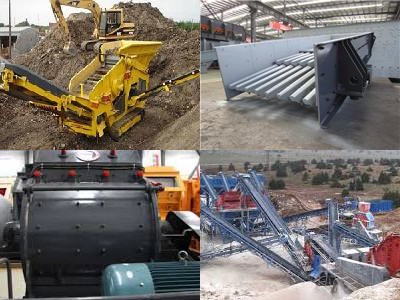
Zenith Company is dedicated to providing top-quality industrial equipment to meet the needs of various industries worldwide. Among the essential components of crushing equipment, crusher wear plates play a crucial role in ensuring optimal performance and longevity. In this article, we delve into the significance of crusher wear plates, exploring their functions, types, and maintenance strategies to enhance equipment performance and extend its lifespan.
Importance of Crusher Wear Plates
Crusher wear plates serve as protective linings that shield crucial components of crushing equipment from excessive wear and tear. They are strategically positioned to withstand the abrasive forces generated during the crushing process, effectively safeguarding against premature equipment failure. Without proper wear plates, vital components such as jaws and liners would succumb to accelerated deterioration, leading to costly downtime and repairs.
In addition to their protective function, crusher wear plates contribute significantly to the overall efficiency and productivity of crushing operations. By minimizing wear on key components, such as jaw dies and cheek plates, they ensure consistent performance and reduce the need for frequent replacements. This translates to improved throughput, reduced maintenance costs, and enhanced profitability for industrial operations, making them indispensable assets in the crushing industry.
Types of Crusher Wear Plates
Crusher wear plates are available in various materials, each tailored to specific application requirements. Common materials include manganese steel, chromium carbide, and tungsten carbide, among others. Manganese steel plates are renowned for their exceptional toughness and abrasion resistance, making them ideal for high-impact applications. Chromium carbide plates, on the other hand, offer superior wear resistance in harsh operating conditions, while tungsten carbide plates excel in cutting and shredding applications.
Depending on the nature of the crushing operation, different types of wear plates may be employed to optimize performance and durability. For instance, jaw plates and cheek plates are commonly used in jaw crushers to protect against abrasive wear, while impact plates and side liners are prevalent in impact crushers to withstand high-impact forces. Understanding the unique characteristics of each type is essential for selecting the most suitable wear plates for specific crushing applications.
Maintenance and Replacement Strategies
Regular inspection and maintenance of crusher wear plates are imperative to ensure optimal performance and longevity of crushing equipment. Periodic checks for signs of wear, such as excessive grooving or thinning, enable early detection of potential issues and prompt replacement before significant damage occurs. Additionally, implementing proper maintenance practices, such as lubrication and tightening, can prolong the service life of wear plates and mitigate the risk of premature failure.
In conclusion, crusher wear plates play a vital role in enhancing the performance and longevity of crushing equipment. By providing robust protection against abrasive forces and minimizing wear on critical components, they contribute to efficient and reliable crushing operations. At Zenith Company, we offer a comprehensive range of crusher wear plates designed to meet the diverse needs of our customers. From jaw plates to impact plates, our high-quality products ensure optimal performance and maximum durability, ensuring unparalleled value for industrial applications.
===OUTRO: