Don't miss our holiday offer - 30% OFF!
What Are The Different Types Of Crushers Available And Their Uses?
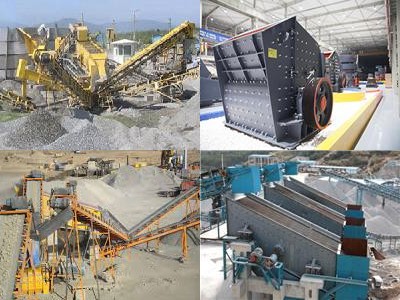
Crushers play a fundamental role in various industries, from mining to construction, by breaking down large rocks into smaller, more manageable pieces. They come in a variety of types, each designed for specific purposes and applications. In this article, we will explore the different types of crushers available and their uses, providing insights into the machinery that drives productivity and efficiency in heavy industrial processes.
Introduction to Crushers
Crushers are mechanical devices used to reduce the size of large rocks, ores, and other materials into smaller pieces suitable for further processing. They operate by applying force to the material to break it apart, often through compression or impact mechanisms. Common types of crushers include jaw crushers, gyratory crushers, cone crushers, and impact crushers. Each type has its unique characteristics and advantages, making them suitable for different tasks and environments.
Primary Crushers: Breaking Down Initial Material
Primary crushers are the first stage in the crushing process, tasked with reducing the initial feed material to a manageable size. They are typically large, heavy-duty machines designed to handle the toughest materials. Jaw crushers, for example, use a fixed jaw and a moving jaw to apply pressure and crush the material against a stationary surface. These crushers are ideal for high-capacity primary crushing in mining and quarrying operations.
At Zenith, we offer a range of primary crushers tailored to meet the needs of our customers. Our Zenith C Series jaw crushers are renowned for their reliability and performance in demanding applications. With features such as optimized kinematics and a long stroke, these crushers deliver high reduction ratios and consistent product quality, making them the preferred choice for primary crushing operations worldwide.
Secondary Crushers: Refining Particle Size
Secondary crushers follow primary crushers in the crushing process and are tasked with further reducing the size of the material to achieve the desired particle size distribution. They come in various designs, including cone crushers and impact crushers, each suited to specific applications. Cone crushers, for instance, utilize a rotating mantle within a concave bowl to crush the material between them, while impact crushers use the principle of impact to pulverize the material.
Zenith’s range of secondary crushers includes our Zenith HP Series cone crushers, renowned for their high performance, reliability, and versatility. These cone crushers are capable of producing finely crushed end products with excellent particle shape, making them ideal for secondary and tertiary crushing applications in mining and aggregate industries.
Tertiary Crushers: Fine-Tuning Output Size
Tertiary crushers are the final stage in the crushing process, responsible for producing finely crushed end products. They are designed to refine the particle size and shape of the material to meet specific requirements, such as for concrete production or asphalt recycling. Tertiary crushers often feature a combination of impact crushing and grinding mechanisms to achieve the desired results.
At Zenith, our range of tertiary crushers includes the Zenith NP Series horizontal shaft impact (HSI) crushers, known for their high reduction ratios and superior particle shape control. These crushers excel in producing consistent, cubical-shaped end products, making them ideal for applications where precise particle size distribution is crucial, such as in the production of high-quality aggregates for construction projects.
In conclusion, the diverse range of crushers available caters to various stages of the crushing process, offering solutions for primary, secondary, and tertiary crushing applications. At Zenith, we understand the importance of selecting the right crusher for your specific needs and applications. With our comprehensive range of crushers and expert guidance, we are committed to helping our customers optimize their operations and achieve their production goals efficiently and cost-effectively.