Don't miss our holiday offer - 30% OFF!
What Are The Key Considerations For Setting Up A Basalt Crushing Plant?
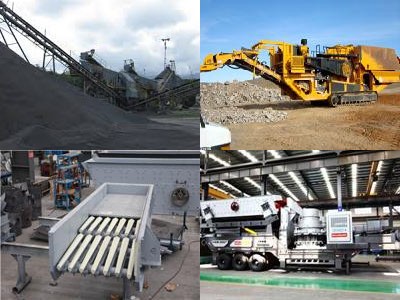
Setting up a basalt crushing plant requires careful consideration of several key factors to ensure efficiency, durability, and cost-effectiveness. Basalt, a dense volcanic rock, presents unique challenges and opportunities in crushing operations. This article, brought to you by Zenith company, a leader in crushing and milling technology, explores the essential aspects of establishing a successful basalt crushing plant.
Understanding Basalt Properties and Crushing Requirements
Basalt’s hardness and abrasiveness demand robust crushing equipment that can withstand intense operational pressures. The first step in setting up a plant is to analyze the material characteristics, including size, hardness, and abrasiveness. This analysis will guide the selection of crushers that can efficiently reduce the basalt to the required sizes without excessive wear. Zenith’s range of jaw crushers and cone crushers are specifically designed to meet these challenges, offering long service life and optimal crushing performance.
The moisture content and the presence of impurities in basalt also affect the choice of supplementary equipment such as screens and washers. Ensuring that the crushing circuit is designed to handle variations in material properties is crucial for maintaining productivity and reducing downtime. Zenith provides comprehensive solutions with its advanced screening and washing technologies that adapt to different material conditions.
Selecting the Right Equipment for Basalt Processing
Choosing the appropriate machinery for basalt processing is critical to plant efficiency. The primary crusher must be capable of handling large feed sizes and achieving high reduction ratios. Zenith’s gyratory crushers are well-suited for primary crushing of basalt, offering high throughput rates and reliable operation. For secondary and tertiary crushing, impact crushers or cone crushers can be used depending on the desired final product size and shape.
In addition to crushing equipment, selecting the right auxiliary machinery, such as feeders, conveyors, and screens, is essential. These components must be optimized to work seamlessly with the crushers to ensure a smooth flow of material through the plant. Zenith offers a range of vibrating feeders and conveyors that are engineered to enhance the efficiency of basalt processing operations.
Operational Considerations and Plant Layout Design
The layout of a basalt crushing plant impacts its operational efficiency and maintenance needs. It is important to design a layout that allows for easy access to key equipment for regular maintenance. Strategic placement of equipment can also reduce material handling costs and improve the overall flow of materials through the plant. Zenith’s engineering team specializes in plant design and can assist in creating an optimal layout tailored to specific operational requirements.
Environmental considerations, such as dust control and noise reduction, are also crucial in the design of a basalt crushing plant. Implementing effective dust suppression and noise dampening technologies not only improves the working environment but also complies with regulatory standards. Zenith offers solutions that incorporate advanced dust suppression systems and noise reduction enclosures to enhance environmental compliance and safety.
Establishing a basalt crushing plant involves careful consideration of material properties, equipment selection, and plant layout. By understanding these key aspects and choosing the right equipment, you can ensure efficient and sustainable operations. Zenith company, with its extensive experience and range of high-quality crushers and ancillary equipment, is your ideal partner in setting up a state-of-the-art basalt crushing plant. Contact us today to learn more about how our products and services can meet your crushing needs.