Don't miss our holiday offer - 30% OFF!
What Is The Typical Process Flow In A Crusher Plant?
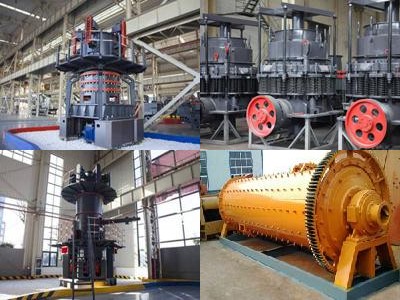
The process flow in a crusher plant is a critical aspect of the mining and construction industries. Understanding the various stages involved in crushing and processing materials can help optimize operations, improve efficiency, and ensure the production of high-quality aggregates. At Zenith, we specialize in providing top-of-the-line crushers, mills, and other heavy industrial equipment designed to meet the demands of modern crusher plants. This article will guide you through the typical process flow in a crusher plant, highlighting the key stages and the equipment used.
Introduction to Crusher Plant Operations
Crusher plants are essential in the mining and construction industries for breaking down large rocks and minerals into smaller, more manageable pieces. The operations within a crusher plant are complex and involve several stages, each with its specific purpose and equipment. Understanding these stages is crucial for optimizing the plant’s performance and ensuring the production of high-quality aggregates.
At Zenith, we offer a range of crushers and mills designed to handle various materials and processing requirements. Our equipment is engineered to provide maximum efficiency, durability, and ease of maintenance, making it ideal for use in crusher plants. Whether you need primary, secondary, or tertiary crushing solutions, Zenith has the right equipment to meet your needs.
The typical process flow in a crusher plant begins with the extraction of raw materials from the quarry. These materials are then transported to the plant, where they undergo a series of crushing and screening processes to produce the desired size and quality of aggregates. Each stage of the process is carefully monitored and controlled to ensure optimal performance and product consistency.
Primary Crushing: Initial Size Reduction
The primary crushing stage is the first step in the process flow of a crusher plant. This stage involves the initial size reduction of large rocks and minerals, making them easier to handle and process in subsequent stages. Primary crushers are typically designed to handle large feed sizes and high capacities, ensuring efficient and effective crushing.
Zenith offers a range of primary crushers, including jaw crushers and gyratory crushers, designed to handle the toughest materials and provide reliable performance. Our jaw crushers are known for their robust construction, high crushing efficiency, and ease of maintenance, making them ideal for use in primary crushing applications. Gyratory crushers, on the other hand, offer high capacity and continuous operation, making them suitable for large-scale mining and quarrying operations.
During the primary crushing stage, the raw materials are fed into the crusher, where they are subjected to compressive forces that break them down into smaller pieces. The crushed material is then transported to the next stage of the process, where it undergoes further size reduction and processing.
Secondary Crushing: Further Material Breakdown
The secondary crushing stage is the next step in the process flow of a crusher plant. This stage involves further size reduction of the material that has already been processed in the primary crushing stage. Secondary crushers are designed to handle smaller feed sizes and provide finer output, ensuring the production of high-quality aggregates.
Zenith offers a range of secondary crushers, including cone crushers and impact crushers, designed to provide efficient and effective secondary crushing. Our cone crushers are known for their high crushing efficiency, excellent product shape, and low operating costs, making them ideal for use in secondary crushing applications. Impact crushers, on the other hand, offer high reduction ratios and the ability to handle a wide range of materials, making them suitable for various secondary crushing applications.
During the secondary crushing stage, the material is fed into the crusher, where it is subjected to additional compressive and impact forces that further break it down into smaller pieces. The crushed material is then transported to the next stage of the process, where it undergoes screening and conveying to produce the final product.
Screening and Conveying: Sorting and Transporting Materials
The screening and conveying stage is the final step in the process flow of a crusher plant. This stage involves sorting the crushed material into different size fractions and transporting it to the appropriate storage or processing areas. Screening and conveying equipment are essential for ensuring the production of high-quality aggregates and efficient plant operations.
Zenith offers a range of screening and conveying equipment, including vibrating screens, belt conveyors, and feeders, designed to provide reliable and efficient performance. Our vibrating screens are known for their high screening efficiency, durability, and ease of maintenance, making them ideal for use in crusher plants. Belt conveyors and feeders, on the other hand, offer efficient material transport and handling, ensuring smooth and continuous plant operations.
During the screening and conveying stage, the crushed material is fed into the vibrating screen, where it is sorted into different size fractions. The sorted material is then transported by belt conveyors to the appropriate storage or processing areas, ensuring efficient and effective plant operations. This stage is crucial for producing high-quality aggregates and optimizing the overall performance of the crusher plant.
Understanding the typical process flow in a crusher plant is essential for optimizing operations and ensuring the production of high-quality aggregates. At Zenith, we offer a range of crushers, mills, and other heavy industrial equipment designed to meet the demands of modern crusher plants. Our equipment is engineered to provide maximum efficiency, durability, and ease of maintenance, making it ideal for use in various stages of the crushing process. Whether you need primary, secondary, or tertiary crushing solutions, Zenith has the right equipment to meet your needs and help you achieve your production goals.