Don't miss our holiday offer - 30% OFF!
Jaw Crusher Vs Gyratory Crusher: Which One Should You Choose?
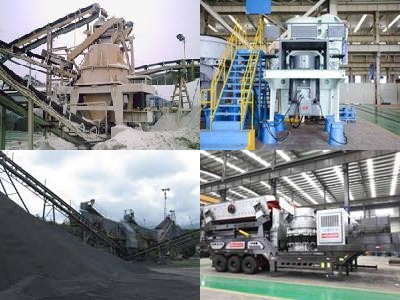
In the realm of heavy industrial equipment, the choice between a jaw crusher and a gyratory crusher is often a critical one, as each plays a distinct role in the production process. Jaw crushers, known for their simplicity and versatility, are commonly used in various industries for primary crushing tasks. On the other hand, gyratory crushers, with their larger crushing chambers and higher capacity, are favored in applications where high throughput and efficient reduction of large-sized materials are paramount. Let’s delve deeper into the workings of these two types of crushers and explore the factors to consider when choosing between them.
Introduction: Understanding Jaw and Gyratory Crushers
When it comes to jaw crushers, their design revolves around a fixed jaw and a movable jaw that together form a V-shaped chamber. This configuration allows the material to be crushed efficiently by applying pressure from both sides. Jaw crushers are highly adaptable and can handle various types of materials, ranging from hard rock to recycled concrete. On the other hand, gyratory crushers operate on a similar principle but feature a conical head and a concave surface, providing a larger crushing chamber. This design enables gyratory crushers to process larger feed sizes and achieve higher capacities compared to jaw crushers.
Comparing Performance: Efficiency, Capacity, and Maintenance
In terms of performance, both jaw crushers and gyratory crushers have their strengths and weaknesses. Jaw crushers excel in their simplicity and ease of maintenance, making them suitable for smaller-scale operations where frequent adjustments are necessary. However, they may struggle with abrasive materials and have limited capacity compared to gyratory crushers. Gyratory crushers, on the other hand, boast higher capacities and are better suited for continuous operation in larger-scale applications. While they require more complex maintenance procedures, their robust design and superior crushing capabilities often outweigh these challenges.
Making the Decision: Factors to Consider and Final Verdict
When faced with the decision between a jaw crusher and a gyratory crusher, several factors come into play. Considerations such as the type of material to be crushed, desired output size, and production requirements all play a role in determining the most suitable option. Additionally, factors like initial investment cost and long-term maintenance expenses must be weighed against the expected performance and productivity gains. Ultimately, the choice boils down to finding the right balance between efficiency, capacity, and maintenance needs. Both jaw crushers and gyratory crushers have their place in the industrial landscape, and the optimal selection depends on the specific needs and priorities of the operation.
In conclusion, whether you opt for a jaw crusher or a gyratory crusher, it’s essential to partner with a trusted supplier like Zenith to ensure you get the most out of your investment. At Zenith, we offer a wide range of crushers, mills, and other heavy industrial equipment tailored to meet your unique requirements. From robust jaw crushers designed for primary crushing to high-capacity gyratory crushers built for demanding applications, our products are engineered to deliver reliable performance and maximum productivity. Contact us today to learn more about our comprehensive lineup and find the perfect solution for your crushing needs.